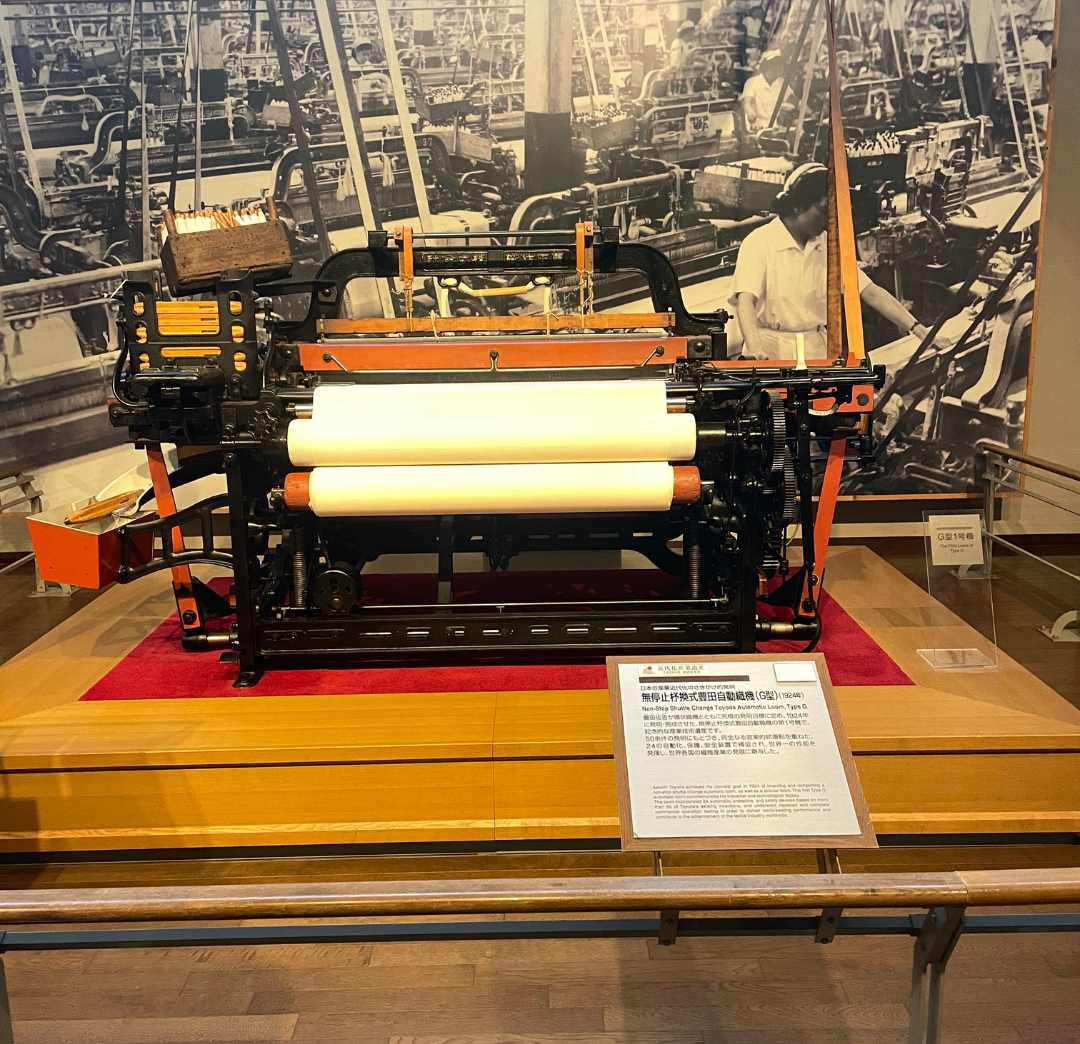
In-depth Exploration of Kaizen Culture : A Benchmark of Japanese Companies
As devotees of the Toyota model
Drawing on our diverse experiences, we encountered a varied landscape: resounding successes with companies that have undertaken profound transformations, but also persistent challenges in sustaining Kaizen over time.
We studied the impediments that Japanese companies may face in sustainably integrating Kaizen into their corporate culture, despite their cultural proximity to Toyota . During our journey through several Japanese cities, here’s what we observed:
Some Who Claim to Be Lean Don’t Always Practice Kaizen.
As in Europe, many companies in Japan use Lean tools without truly adopting the Kaizen culture. This is evidenced by:
- Japanese companies that make a few improvements annually, often under the guidance of external experts, but without any real commitment from operators in the field neither autonomous problem-solving.
- Some have a system that is close to TPS but does not fully integrate the Kaizen dimension.
Despite these challenges, it’s important to note that Respect, Cleanliness, and Visual Management are much more highly developed in Japan than in Europe or America.
For those Who Adopt Kaizen… It’s Remarkable
We have had the privilege of visiting companies, including SMEs, that have been diligently practicing Kaizen for over 50 years:
- The Kaizen state of mind is palpable: general participation and daily commitment are evident from the moment we arrive.
- The innovations proposed by employees are ingenious, simple, clever, and obvious—providing a constant source of enthusiasm at every stage of our visit.
- The production lines are remarkably efficient and flexible, based on adaptive and scalable solutions.
We found that when Kaizen is fully integrated, it becomes the very strategy of the company, perfectly aligning the company’s vision with its operational strategy.
One More Thing
For those who have made it this far, I’d like to offer a numerical comparison of one of the key TPS indicators: the number of proposals per employee (PPC).
While Toyota boasts an impressive rate of one PPC per day, some of the organizations we have worked with achieve a respectable PPC per week. However, the most advanced companies we visited in Japan reach an extraordinary level with one improvement proposal per person per week, company-wide!
Top Organization (company division) EUROPE: 1 PPC per week
Top Companies JAPAN: 1 PPC per week
TOYOTA: 1 PPC per day
This comparative analysis highlights the crucial importance of the sustainable integration of Kaizen into corporate culture. Japanese companies that have succeeded in this integration enjoy higher employee commitment than their competitors.